If you have met me or seen my car, you will already
know it is not destined for any concours parade. It
is my car, built by me, for me. It has always been
my means of escape from my desk job and I enjoy
the spanner-ing as much as the driving. Hence
why I am always taking things apart, modifying and
(hopefully!) improving things.
For many years my car was fuelled by means of
a Weber DCOE carburettor. It had that glorious,
distinctive noise and was great for general and
open, fast road driving. But after years of messing
with and enjoying the DCOE there were two quirks
that became a little wearisome. Firstly, the lack
of a proper choke and it’s general lumpiness when
cold put me off using the car in the colder months.
Secondly, a slight hesitation in the transient
response that was only really an issue when really
pushing on out of tight and twisties at sprint and
hillclimb courses.
The above, plus the aforementioned compulsion
to build, tinker and learn new things (I am a
mechanical design engineer, it’s just what I do!)
and a desire to have something unique, lead me
to devising and building a fully programmable
electronic fuel injection system for my 1500.
Fuel Injection Systems 101
I imagine there are those who think an electronic
fuel injection (EFI) system is totally alien, possibly
even sacrilegious! So the following is a fuel
Out with the old - DCOE carb’ removed.
injection 101 to try and demystify things a little. In
a basic system, we need seven things:
1. A fuel rail and injectors: The fuel rail acts as a
pressurised “float bowl”, providing a reserve of fuel
behind the injectors. Injectors, to me, is a bit of
a misnomer as it makes them sound like syringes
that “push” the fuel into the engine. Actually, the
injectors are simply electrically controlled valves
that switch on and off and high speed. When they
are energised, they open and the pressurised fuel
in the fuel rail flows flows through the injector
into the manifold. The ECU (see below) is able to
control how long the injectors remain open down to
a resolution of 0.1ms (0.0001 seconds) allowing for
very precise control of the volume of fuel flowing
during the cycle.
2. A means of sensing engine load/demand: Either
a manifold air pressure (MAP) sensor or a throttle
position sensor. Fairly self-explanatory, these
measure the pressure (vacuum) inside the manifold
and the angle of the throttle respectively.
3. A means of sensing the engine speed (rpm):
On my setup this is done by sensing the trigger
pulse from the distributor/coil, via some signal
conditioning circuitry.
4. A high pressure fuel system: Carbs only require
a few psi pressure, whereas an injection system
requires a much higher pressure (typically 43.5 psi,
3 bar) to push the fuel through the injectors and in
Laying out the main parts of the system circa.December 2019.
the process atomise the fuel. So a new pump, a
pressure regulator, a low pressure return to the tank
and all the associated plumbing is needed.
5. An electronic control unit (ECU). The ECU is
simply a small, specially designed, computer and
what makes the system EFI rather than just FI! For
example, the TR6 PI (petrol injection) system, was
without the E, as it was controlled by mechanical
means, not by a computer.
6. A manifold to hang everything off.
7. Some wires to link all the electrical bits together.
With this we could run the engine if we already had
a well defined fuel map. A map is the term used
for the settings and equations contained within
the ECU - relating the load, engine speed and fuel
requirements together.
However, we add a few more sensors to expand the
range of control we have and allow easier tuning:
1. A manifold air temperature (MAT) sensor, for
measuring the temperature and thus density of the
air entering the engine.
2. A coolant temperature sensor, to allow the ECU
to calculate and control the warmup enrichment
requirements, effectively replacing the choke.
3. A wideband lambda sensor (also known as an
O2 sensor). Which “sniffs” the composition of the
exhaust gases and is thus able to tell how rich or
lean the engine is running.
This is where the system comes into it’s own,
using all these sensors and the clever computer
software the whole system is able to self learn how
The ECU, small enough to fit in your hand. I had soldered all the components.
much fuel it needs and continues to adjust itself
for maximum performance for any given speed and
load.
Where to Start?
The build sort of started in the summer of 2019,
as I started sketching out detailed plans and
accumulating parts. Parts were mostly found
through eBay, sorting price low to high and looking
for bits from cars that were of similar power output
(at last check, I had 101hp at the crank, but I have
built in head room to go up to 120). The throttle
was from a rover K-series engine, the injectors
from a Land Rover V8, the temperature sensors are
Ford, it is fuelled by a Bosch-a-like fuel pump, and a
controlled by a Speeduino ECU.
As the plumbing, wiring and manifold were all going
to have to be custom made, and the software/ECU
can be calibrated to work with whatever it is given,
the mis-match of parts wasn’t ever an issue.
New fuses, relays and electrical spaghetti.
The working system circa July 2020. Needs some
tidy ups, but I am too busy driving it now!
Breaking Ground
Probably the most pivotal part of the project was
the manifold, as it is what everything else attaches
to and the interface between the new system and
the old engine. I was able to draw up the flange
in a CAD (computer aided design) package and
have it laser cut from stainless steel. The rest of
the manifold was fabricated from various sizes of
stainless steel tubing. The fabrication was a bit
rough and ready (I am not really a fabricator!) and
done using nothing but a grinder and Dremel for
cutting and shaping and gummed together with my
90-amp hobby MIG welder! It was labour intensive
and is a bit shoddy looking, but it is functional
and kept me entertained during a brief spell of
unemployment!
Once the manifold was near complete, the strip
down of the car began, so I could begin test
fitting things. It was a bit of an iterative process,
positioning things, finding clashes and reconfiguring until a reasonable and tidy compromise
was found.
The Brains Behind the Outfit
The REALLY clever stuff is contained in the ECU and
associated software/programming. Fortunately, the
clever boffins in the world have done all the hard
work already and wrapped up all the electronics
and software stuff into nice easy to use packages.
Talking of packages, the ECU itself was a fun
mini-project. To keep costs down I bought the
self assembly version of the Speeduino ECU. This
comes as a box containing about 100 zip look bags
of various components and a circuit board. It took a
couple of evenings to solder all the tiny components
to the PCB (without any real instructions as to
what went where!). Another couple of evenings in
New decals and vents ensure my car isn’t confused
for a smokey old carburettor car!
front of the computer allowed me to test the basic
functions. Amazingly, it all worked first time!
The ECU connects to a laptop via a USB cable in
order to tune and alter settings. Settings can be
changed whilst the engine is running, which makes
it extremely flexible and easy to tune and once
things are right, the settings can be permanently
written to the ECU and the laptop left at home.
To tie all the electrical gubbins together I had to
make a loom. I found this very enjoyable to make
and it took a few evenings work. Not difficult
with the right tools but you can’t rush it. A lot of
people are scared by electrical/electronic systems.
Which is understandable, as you can’t see it
working. But I look at it differently. I find them
strangely therapeutic to construct, work with and
trouble shoot. You have to be very methodical with
electrical circuits. You can’t bodge them - they
don’t work like that, and problems have to be
solved with “intelligence” because the problem isn’t
usually immediately visible.
Power for the new systems is controlled through a
pair of fused relays and a new six way blade fuse
box. I think I have to be careful driving at night for
the time being, because I have calculated that with
all the additional electrical loads I am near the limit
of the original alternators power output. Having
lights on might tip me over the edge!
The Birth, Teething Problems and Refinements!
With everything welded, soldered, plumbed, wired
and bolted together, the first start was rather
uneventful! Turn the key and it worked, albeit a
little rough! After the adrenalin had subsided I was
able to dial in a reasonable idle and have a few runs
up and down the road. Even without much tuning
the engine was super smooth, lively and tractable.
After that, so the theory goes, you plug in a
laptop and hit the “Autotune” button and the
software optimises the fuelling required based on
assumptions that are generally the same for all
engines and live data from all the sensors.
But practice and theory don’t always align!
The first few longer test runs were not entirely
successful. Each time I went out, the car started
to run increasingly rough after about 20 minutes.
The first time I manage to get back and parked up
in the garage before it died, the second time, it died
whilst I was opening the garage and I had to push
it in. The third time (I should have learnt by this
point), it coughed and died about 50 metres from
home. There were a lot of twitching curtains as I
embarrassingly pushed it the remaining distance
and into the garage!
I jumped to the conclusion that it was the fuel
getting too hot in the rail due to the proximity of the
rail to the exhaust manifold and the fuel rail being
made of an excellent heat sink material (copper).
Therefore, I set about heat wrapping the exhaust
and fuel rail. In the process of doing so, I noticed
a coolant leak near the heater box, so perhaps this
was causing the engine to overheat? Either way,
with the leak fixed and the exhaust wrap in place
the problem hasn’t recurred and the wrap has
noticeably helped under bonnet temperatures. An
hours full chat blat, without issue, when it was 30+
degrees, was the proof of that.
The second major problem manifested itself as
the car being unwilling to accept high loads and/or
high revs without going way lean and popping and
banging like the royal artillery regiment! The data
logging capability within the software showed that
the ECU was continually sensing this lean condition
and opening the injectors for longer and longer to
try to add more fuel until the injectors were maxed
out (always open).
After some over analysis of the data logs I jumped
to the conclusion (seeing a theme here?) that I
needed bigger injectors. Injectors were purchased
and installed and still the same problem! Eh?!
Well, long story short – check the basics first. I
tested the fuel pump flow rate and it was barely
dribbling out of the end of the hose. Certainly not
flowing at the pump rated 135 L/hour! The tiny fuel
filter I had carried over from the carburettor system
was totally clogged and the pump was struggling
to keep up with demand. With an injection system,
the pump runs constantly at full speed and anything
in excessive of three bar pressure and the required
flow is recirculated back to the tank via a pressure
regulator. This means that the old filter was tryingto cope with filtering about four tanks (135L) of
fuel an hour and a whole load of muck was now
being washed out of the tank and being caught by
the filter. In hindsight it stood no chance. A new,
much bigger and purpose designed filter solved
this and concluded weeks of frustration and head
scratching. The car hasn’t missed a beat since.
Finally, I somehow knackered the starter motor
beyond redemption whilst trying to set up the
starting sequence and idle mixture. It was only 50-
odd years old, pah! Rubbish quality Lucas parts!
Driving
Aside from learning something new, the intention
of the conversion was to improve the transient
response, idle and all round driveability of the car,
all things that despite years of messing I never got
perfect with the previous DCOE set up.
Once the above issues were sorted, the Autotune
feature in the software worked brilliantly and the
engine got better, smoother and more powerful the
more and more I drove it as it constantly refined the
fuelling requirements on the fly. Whilst the tuning
process is ongoing, it is already a step up from
the carburetted setup. Cold starts and running
are much improved and general driving is super
smooth. The acceleration enrichment curves still
needs some work to really perfect the transient
responses. But doing so is a little more difficult as
I need someone to drive the laptop whilst I drive the
car!
I would like to get it on a rolling road at some point
to see how it compares to the old system. I don’t
expect to see much change in the headline figures,
but it will be interesting to do the comparison.
From there I plan for a few more engine
enhancements to try to bump power up to 110+
hp, including adding a fully mapped ignition and a
lumpier camshaft. With precise electronic control
of the fuelling and ignition timing I hope that even
with a big, lumpy cam, I won’t lose out too much in
terms of low speed driveability.
Or maybe I could just whack a turbo on it! :-)
If you would like more details on the project, I did
a short series of youtube videos on the technical
details of the setup, search for “Midget 1500 Fuel
Injection”. Or, drop me a message via Facebook.
Cheers, happy Spridgeting!
Malc Le Chevalier
Saturday 10 October 2020
Gear Lever Grommet - Neck UP or DOWN
All Sprites and Midgets built before the arrival of the “face lifted” cars (HAN10 and GAN5 respectively) were given a flexible circular rubber grommet (part number ACA_5208) to seal their gear lever and gear lever turret. No-one disputes this fact. What is very often hotly disputed is how this grommet was installed at the factory: was it “neck-up” or “neckdown”? And why on earth is the strong opinion on this matter so polarised between the Northern and Southern hemispheres? In my experience, there is no more emotive subject associated with our cars: no other topic is able to generate so much animated discussion and produce so many raised hackles. In what follows, I hope to restore calm, logic, law and order to this matter and I begin by reminding everybody that everything is upside down in the Southern Hemisphere. Unless you are a member of the Flat Earth Society, you will know already that Australia is ‘down under’; its water goes the wrong way down plugholes; its sun travels scarily from right to left, pointing north at midday; its stars at night twirl the wrong way; the man in the moon is upside down; runner beans grow in a clockwise direction. The Australian gear lever grommets are upside down too, but I am leaping ahead of my story: we must first look at some facts. While we take this look, the misguided members of that strange Flat Society should instead fly from
Heathrow to Melbourne, watch the moon flip 180º in 24 hours (one of life’s great experiences), then try to explain that flip with their flat theory.
Photographic evidence can help us - but which photographs precisely? In the Northern Hemisphere (Abingdon in particular), the trouble is that very early pre-release and press photographs of Mk1
Sprites show gear lever grommets randomly distributed, sometimes “neck-up”, sometimes “neck-down”. So, if one chooses carefully and very selectively from this vast collection of early material (the launch of the Mk1 Sprite was explosive in the extreme), it is very easy indeed to make a very strong case for either a ‘neck-up’ or a ‘neckdown’ gear lever grommet. For example, those who believe it should be ‘neck-up’ often point to the terrific BMC movie1 of Roy Salvadori driving PBL_75 “neck-up” at Silverstone in the wet with commentary by John Bolster (“You’ll never tire of driving a Sprite”). Others, studiously ignoring Roy, instead point to photographs of brand new ‘neckdown’ Mk1 Sprites taken about the same time Roy’s movie was shot in 1958 by British Pathé.
Two early photographs of brand new Mk1 Sprites (note the utterly pristine mats): one “neck-up” (top, provenance unknown); the other “neck-down” (Photo C081280, courtesy BMHIT archive). In the Northern Hemisphere, order emerges from this blushing mess of gear lever grommet confusion if one ignores completely the early photographs and examines later ones taken after the Abingdon production line had settled down, after it had solved the worst of its prodigious initial teething troubles (the most serious requiring extra gussets to strengthen the body shell and cars travelling backwards up the production line). With very few exceptions, later photographs show the gear lever grommet ‘neck-down’, in complete agreement with the orientation illustrated in all variants of the original production factory Parts Lists and Owner’s Handbook.
Perfect in every detail: a brand new Mk2 Sprite at Abingdon, with gear lever grommet ‘neck-down’. For the later Northern Hemisphere cars (beginning with the Mk2 Sprites and Mk1 Midgets) the evidence is quite simply overwhelming: the Abingdon factory installed the gear lever grommet with its neck down as surely as the Healeys in Warwick watched the sun rise on the left while their runner beans grew anticlockwise. To right - a pre-production version of the Mk1 Sprite’s Owner’s Handbook (top, note the strange steering wheel) shows the gear lever grommet ‘neck up’. All production versions (bottom) show the same grommet ‘neck-down’ Why then do all Australian Sprites and Midgets wear their gear lever grommets ‘neck-up’? Well, rather than looking up into the inverted bowl of the Southern Sky for help, the answer is almost
certainly to be found at ground level, within the Pressed Metal Corporation factory at Enfield (New South Wales) where, to avoid excessive import taxes, the CKD2 kits for Mk1 Sprites were assembled for the Australian market. Precisely why this factory decided to go ‘neck-up’ with its grommets is a mystery, the whole affair is shrouded in doubt. We do know that at least one of the first Mk1 Sprites to reach Australia (a very early car, an import, not a CKD kit) had a ‘neck-up’ grommet so perhaps this influenced matters, we don’t know. Alternatively, perhaps the captains of the Enfield
factory simply thought the grommet looked better ‘neck-up’, even though the rubber surface looks rougher and the rubber tends to tear more that way. We don’t know that either. What we do know is that it would be an extremely brave concours judge who deducted points for an ‘upside down’ gear lever grommet in one of our cars, no matter the hemisphere and no matter which way the thing is pointing. Of course, in the final analysis, it is the owner’s own choice: the grommet does work both ways and many people do prefer the ‘neck-up’ look. Summing up, no owner can do very wrong if they go ‘neck-down’ when they are ‘up’ in the Northern hemisphere, and ‘neck-up’ when they are downunder.
John E. Davies (Member 3443)
Subscribe to:
Posts (Atom)
1500 DIY Fuel Injection Conversion
If you have met me or seen my car, you will already know it is not destined for any concours parade. It is my car, built by me, for me. It h...
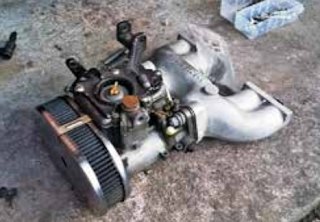
-
If you have met me or seen my car, you will already know it is not destined for any concours parade. It is my car, built by me, for me. It h...
-
All Sprites and Midgets built before the arrival of the “face lifted” cars (HAN10 and GAN5 respectively) were given a flexible circular rubb...